統合発泡アルミニウム成形プロセスシミュレーションにおけるFLOW-3Dのパラメータ適応
このアプリケーションノートはエアランゲン・ニュルンベルク・フリードリヒ・アレクサンダー大学材工学部、金属学科のJohannes Hartmann氏とVera Juchter氏によって投稿された。発泡アルミニウムは、制動性や高いエネルギー吸収、質量に対する曲げ剛性などの面で優れた特性を示す[1]。剛性は耐荷重特性や軽量構造において特に魅力的である。この重量比剛性とより良い荷重伝達を増加させるために、Aluminum Foam Sandwiches(AFS)で達成されるような高密な被膜が必要である[2]。
エルランゲン-ニュルンベルク大学金属学科では、硬い被膜を持ち、内部が発泡状でその間が緩やかに変化する発泡アルミニウムを生成するために、ダイカスト鋳造の修正である統合発泡モデル(IFM)の開発が行われた(図1参照)。
このプロセスはポリマーの発泡射出成形から開発され、硬質被膜を有する複雑な発泡部品の大量生産では高い費用対効果が見込める。このノートで解説するシミュレーション技術は、プロセスパラメータの選択の補助として本プロセスをモデル化するために利用できると考えられる。
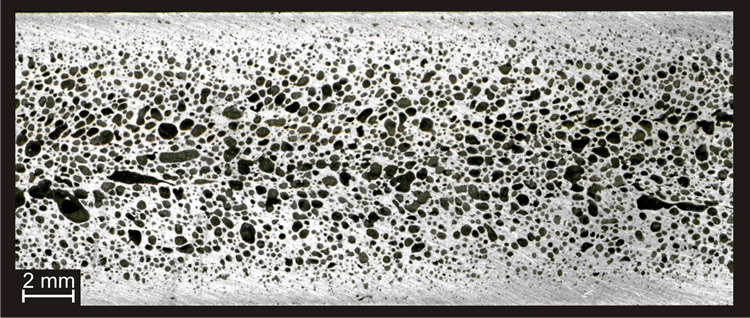
図1. 硬質皮膜を有する統合発泡アルミニウムの断面図。発泡コアと同様に、
孔の密度減少と小孔化の遷移領域。
統合発泡アルミニウム成形技術
ある量の発泡剤(水素化マグネシウム、MgH2)がランナーシステムに設置され、ショットチャンバーはアルミニウムで満たされる(プロセスサイクルの概要を図2に示す。本プロセスは文献[3]で詳述されている)。ピストンによる射出で、この粉末は乱流に乗って鋳型の中に連行される。技術改良型”高圧統合発泡成形(HP-IFM)”の場合では、部品は標準のダイカスト法から知られているように高い周囲圧力で満たされ、優れた表面品質を保証する。溶融金属は、金型の焼戻し表面から硬い被膜として凝固を開始する。数ミリ秒後(いわゆる遅延時間)、鋳型がコアプラ-システムを介して開かれ、水素化マグネシウム粒子の熱分解と水素放出により内側の半凝固領域から発泡が開始し、体積は局所的に増加する(圧力は減少する)。全ての発泡剤粒子は発泡の核であり、同時に成長している周囲細孔の反発圧力と釣り合うまで発泡が続く。形成されるセルの壁はアルミ合金を主として固められた粒子により安定している。いわゆる内因性の安定化である[4]。
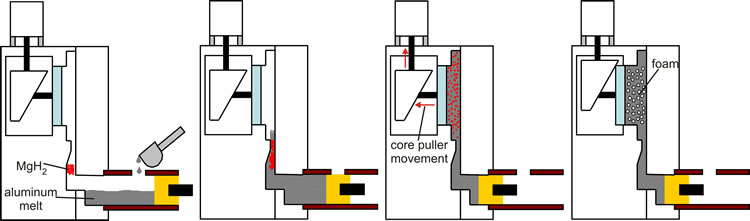
図2. アルミニウムの“高圧統合発泡成形(HP-IFM)”のプロセスサイクルの概要
鋳造部品の体積全体で均一な泡形成のための前提条件は、分解開始の瞬間における粒子の良好な分布である。さらには、一方では発泡剤を巻き込むときの溶融金属の温度は、水素化マグネシウムの分解機構にとって重要であり(図3参照)、また発泡時の固相量を決定する。分解が不十分な固化した粒子は毛細管力による溶融金属の排出で孔の粗大化を引き起こすため、隣接する孔の形成において不安定な要因となる。しかしながら、非常に多い量の固相は、マトリックスの剛性を向上させ、成長している細孔の球状化を妨げる構造の原因となる[2]。
![図3. Johnson-Mehl-Avramiの手法によって計算された溶融温度に対する水素化マグネシウムの分解曲線[2]。](../../wp-content/uploads/2014/02/fig3.jpg)
図3. Johnson-Mehl-Avramiの手法によって計算された溶融温度に対する水素化マグネシウムの分解曲線[2]。
微細セル統合発泡アルミニウム―プロセス限界へのアプローチ
統合発泡成形プロセスのシミュレーションには、新しい部品設計の成形充填特性を調べる強力なツールとしてだけではなく、粒子の巻き込みを予測し、コストの掛かる多くの試験を節約し、発泡成長の条件を決定することができる。
現在の研究の目標は、ポロシティレベルを一定に保ちながら、細孔サイズを減少させることである。数値流体力学(CFD)シミュレーションは、現在のプロセス限界にできるだけ近い情報を取得し、さらにそれらを推し進めることができると考えられる。発泡形態の改良は機械的性質において、微小散乱のある均質的な構造を生むだけではなく、機械的性質が限られた要素で決定される薄い部品の生産も可能とする。この目的は溶融金属内での高い粒子分布と合体の少ない安定した細孔成長により達成できる。
実用的な統合発泡成形実験に対するシミュレーションパラメータの適応
粒子の挙動や温度場の信頼できる予測のためのCFDシミュレーションを使用できるようにするため、異なったシミュレーションパラメータは実際の実験と一致するように調整することで決定しなければならない。最後に、統合発泡部品は30から130msecの遅延時間を変えることで生成される。ここで発泡形成は型の膨張や孔の成長開始の瞬間において固相率がある割合を超える場合1 は不可能となる。これはダイ温度と他の選択されたプロセスパラメータに応じて軸切片と傾きを持つ特徴的な、いわゆる凝固曲線につながる(図4参照)。熱伝達係数(完全に固化した金属だけでなく、完全に液体の金属の値)を変化させることにより、合金AlSi9Cu3(Fe)のための鋳造サイクルをシミュレートし、実験的な凝固曲線を合わせこむことができる。この目的を実現するために、ピストン動作前の実際の温度分布を表現するため、ショットチャンバーへの溶融金属投入までシミュレーションを拡張する必要があった。温度はショットチャンバーに置かれた熱電対によって局所的に計測され、シミュレーションと実測が正しく一致した。また、充填中における鋳型表面の温度についても時間経過に合わせてシミュレーションの結果と相関がとれている。
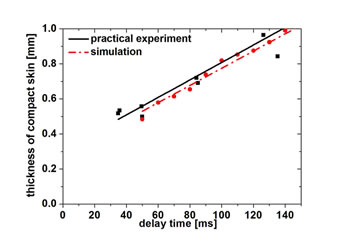
図4. 実際の凝固曲線(黒)とシミュレーションでの固化被膜の成長速度(赤)の比較によるFLOW-3D v9.4での熱伝達の調整。
第2段階では、充填前のピストン停止時におけるシミュレーションと実験との比較によって、表面張力や凝固抵抗係数など溶融流動挙動を決めるパラメータの調整を行った(図5参照)。シミュレーションでの溶融金属の流れは実際の試験と一致するようにパラメータが設定される。
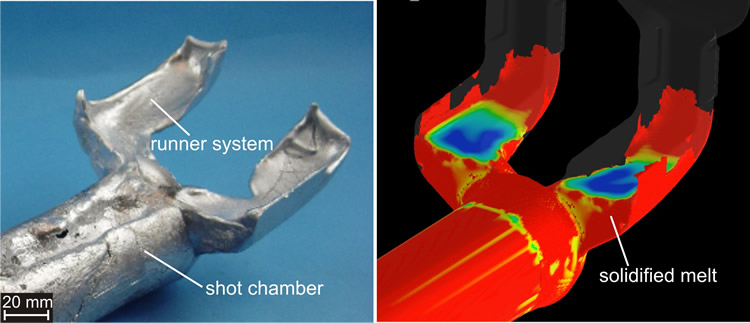
図5. 実験(左)とシミュレーション(右)の比較による表面張力などのパラメータ調整。
溶融金属の流動特性と同様に冷却特性を定義した後、粒子の巻き込みがシミュレートされる。正確な粒子/流体の相互作用を含むシミュレーションのために、粒子抵抗力などの粒子定義パラメータが調整されている。ここではX線透過による比較が用いられ、アルミニウムに対してX線特性の高い対比となる銅や鉄の粒子が水素化マグネシウムの代用として使用されている(図6参照)。シミュレーションの結果は実験と良く一致しており、プロセスパラメータの関数としての粒子分布は信頼の高い予測ができる。
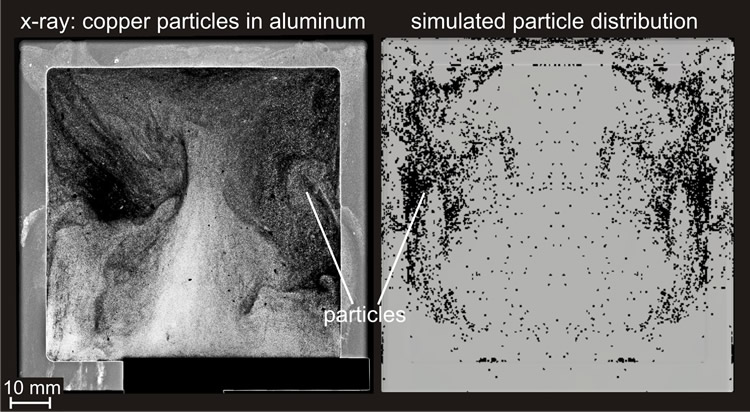
図6. 粒子/溶融金属の相互作用に影響を与えるパラメータ調整。X線透過実験(左)と銅粒子の連行によるシミュレーション(右)の比較。
1 評価基準は固相率であり、ここでせん断強さや発泡成長の抵抗が急激に上昇する。
結言
概してFLOW-3Dは実際に生産する前に新しい統合発泡部品の製造において潜在的な弱点を調べるための重要な手段であることを実証することができた。このような方法で、低温流れや未充填のない良い充填と発泡剤の分布を保証することができる。さらには、温度場の正しい表現により、高密な被膜形成や水素化マグネシウム(また、細孔形成条件なども)の分解特性を推定することができる。これは、統合発泡構造に関して顧客の要求を満たすために、プロセスパラメータを定義するための可能性を提供する。
参考文献
[1] C. Korner, R. F. Singer, Adv. Eng. Mater. 2000, 2 (4), pp. 159-165.
[2] C. Korner, in Integral Foam Molding of Light Metals – Technology, Foam Physics and Foam Simulation, Springer, Berlin, Heidelberg, Germany 2008.
[3] H. Wiehler, C. Korner, R. F. Singer, Adv. Eng. Mater. 2008, 10 (3), pp. 171-178.
[4] J. Hartmann, A. Trepper, C. Korner, Adv. Eng. Mater. 2011, 13 (11), pp. 1050-1055.
※出典参照 : FLOW-3Dニュース2012年 夏季 アプリケーション・ノート